在化工、石油等行业中,精馏设备作为核心单元操作之一,其能耗往往占据整个生产过程的半壁江山。随着全球能源危机的日益严峻和环保法规的不断加强,
精馏设备的节能降耗已成为行业关注的焦点和绿色化工的必由之路。
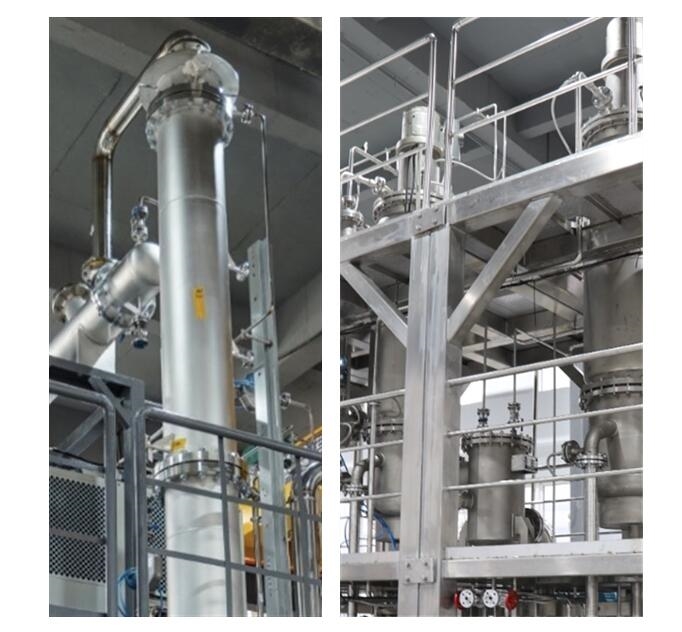
精馏设备节能降耗的关键在于技术创新和优化设计。首先,通过优化精馏塔的结构和操作参数,如选择合适的塔板类型、塔板间距和塔的高度,可以显着提高塔的分离效率,降低能耗。同时,合理调整进料位置和回流比,也是实现节能降耗的重要手段。这些措施不仅能够有效减少能源消耗,还能提高产物质量和稳定性。
此外,热集成技术也是该设备节能降耗的重要途径。在精馏过程中,不同馏分之间存在热量差异,通过合理安排进料和回流,可以将这些热量差异用于彼此加热,从而减少额外的能源消耗。例如,利用塔顶余热的再利用,可以转化为低压蒸汽进行直接供热或用于制冷、发电等,实现能量的多级利用。
热泵技术作为另一种高效的节能手段,在精馏设备中也得到了广泛应用。热泵能够将低位热能转化为高位热能,从而在精馏过程中将塔顶蒸气的热量转化为塔底所需的热量,显着降低能源消耗。同时,强化传热技术和智能控制技术的应用,也进一步提高了设备的传热效率和操作稳定性,为节能降耗提供了有力支持。
值得一提的是,近年来国内外还开发并应用了一些新型节能型耦合精馏塔,如反应精馏塔、热耦合精馏塔和隔板精馏塔等。这些新型精馏塔通过内部结构的优化和能量耦合技术的应用,实现了更高的分离效率和更低的能耗,为设备的节能降耗开辟了新的途径。
综上所述,精馏设备的节能降耗是绿色化工的必然要求和发展趋势。通过技术创新和优化设计,我们可以实现精馏过程的能效提升和资源节约,为可持续发展贡献力量。未来,随着科技的不断进步和环保意识的不断提高,精馏设备的节能降耗将会取得更加显着的成效。